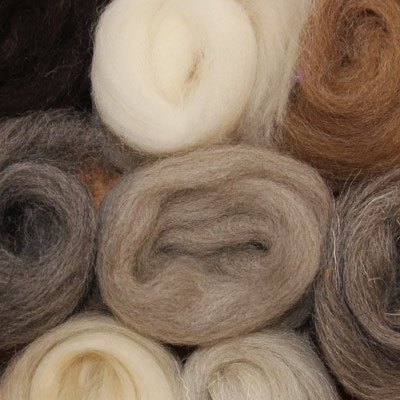
Advancements in fleece
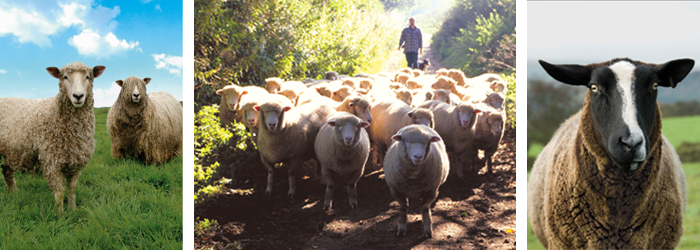
In the 13th century, the industry peaked and raw wool became a prime export being shipped all over the world. The material powered a domestic industrial age of textile making and carpet production. Technological advances in clothes manufacturing, rise of synthetic materials, globalisation, a surge of imports from China and Australia, as well as a decline of manufacturing eroded British wool trade.
Wool started to be looked at as a by-product about 10 years ago and because it was no longer economically effective to lug them to the market, farmers began burning fleeces. This was the time when husband-and-wife designer duo, Hannah and Justin Floyd decided to try to come up with a new product. Floyd, a product designer, mixed wool with bio-resin to create a hardy and attractive material, which resulted in a sustainable alternative to fibreglass, Solidwool, which is being used in products from glass frames to chairs. The pair approached the British Wool Marketing Board (BWMB) to secure the raw materials to make the composite. BWMB recommended they use Herdwick wool. The grey, blue Herdwick wool with its white guard hairs made the perfect raw material.
Plymouth University tested the material and found it to be stronger than all other natural composites, including hemp. In February, it was made commercially available and now there are many partnerships in the works, from Derbyshire-based Blok Knives, to the cold water surf brand Finisterre, which uses it for a comb to wax surfboards.
Innovations galore
Tim Simmons another innovator stumbled into the wool business. His sister-in-law bought part of a wool felting business four years ago when a friend was unwell. The felts were used for insulation, however, Simmons and his wife Marty were keen to find more valuable applications for the material to differentiate their business from companies such as Therma Fleece in Cumbria. These companies do a great business with wool insulation products, which is a natural alternative to synthetic rockwool or stonewool.
Simmons’ company, Woolly Shepherd, makes woollen sound absorbers. The absorbers such as such as the cloud-shaped ‘acoustic cloud’, hang from the ceiling and absorb the sound of neighbours’ walking on hard-wood floors. Simmons says they use only British wool because farmers get a raw deal. They could buy wool at cheaper prices from China but the coarse wool is helpful their products and revenues have doubled year-on-year since 2013.
These and other such inventions are helping the British wool industry stay afloat and production is around 30 million kilos a year. Exports have gone up and as per BWMB says after the decade old slump, they are finally witnessing a turnaround.